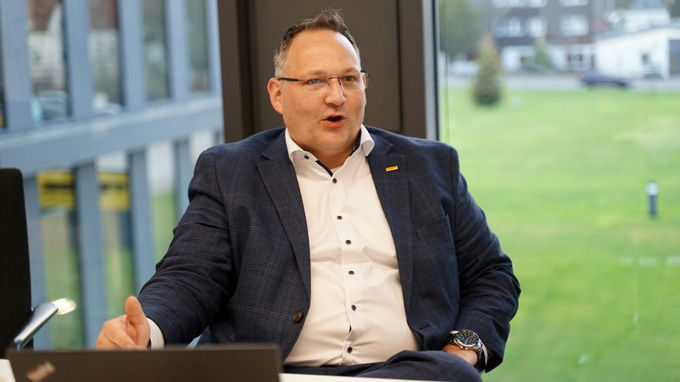
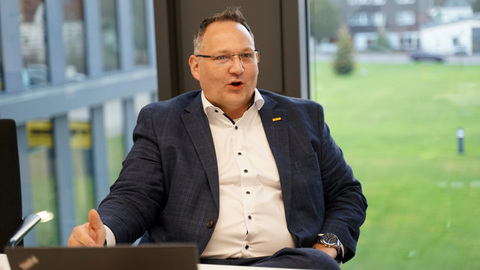
Digitalized Conveyor Lines as a Success Factor in Machine Building and Intralogistics
Turck’s intralogistics specialist Frank Morassi on the trend towards digitalized conveyor lines
»Modularization and digitalization are among the top issues in mechanical and plant engineering, not least in intralogistics. The best way for today’s users to meet their customers’ rapidly changing requirements is with modular and flexibly scalable conveyor lines. For these to also offer high availability and work ideally with zero pressure accumulation, an efficient digitalization strategy is unavoidable. The trend is moving away from massive, centrally controlled and driven lines towards decentralized control modules and roller drives directly in the field.
The digitalization of the conveyor line and decentralized, cabinet-free control concepts offer a number of advantages. First of all, there is the benefit of simple scalability. If requirements change, digitalized conveyor modules can be quickly combined to create new route layouts, all with very little wiring effort. Smart I/O modules on the conveyor modules not only provide the control intelligence but also inputs and outputs for sensors and actuators, the latter primarily in the form of roller motors. All devices are supplied via robust IP67 power supply units on the modules for which the voltage is looped through via M12 power cables thanks to the line topology. The connected motors require a power supply of either 48 or 24 volts.
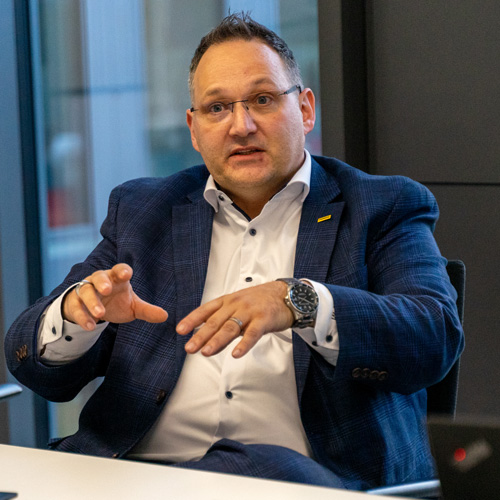
Decentralized control modules significantly reduce data traffic and also enable short cycle times. Conveyor lines fitted like this benefit from improved energy efficiency as it is possible to switch off motor rollers that are not in use almost immediately.
Last but not least, the digitalization of the conveyor line also increases its availability. Smart control modules also record in the background the status of the connected motor rollers. An increase in the power requirement above a standard value indicates an imminent failure of the drive in the foreseeable future. If these values are continuously monitored, the system issues a warning in good time, allowing the user to replace the defective motor rollers as part of a planned maintenance measure. In this way, unplanned downtimes can be kept to a minimum.
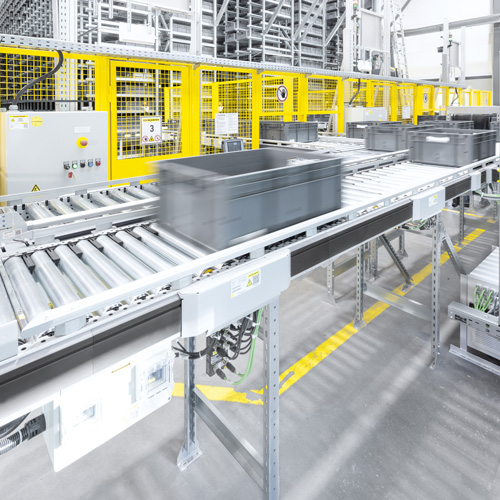
Turck’s response to the trend towards the digitalization of conveyor lines is a sophisticated portfolio of robust IP67 block modules. The I/O modules of the TBEN-S and TBEN-L series for signal distribution directly on the conveyor system or the TBEN-L-PLC IP67 PLC for autonomous control directly on the module are increasingly being used in intralogistics systems. A further IP67 module, which was developed specifically for controlling roller motors, is another important component for making conveyor systems more flexible and modular. Users of Interroll drum motors have been able to use Turck’s TBEN-L-4RMC module for some time now. It controls the motor rollers via the CAN interface and the Turck Multiprotocol enables it to communicate automatically with the controller via one of the three Ethernet languages Profinet, EtherNet/IP or Modbus TCP. The module can now also be used for motors from the manufacturers MPC and MTA.
Actuators or sensors can be connected via four digital inputs or four universal inputs or outputs (DXP ports). The user can execute various pre-programmed control routines via the module’s four CAN ports, for example to easily set up zero pressure accumulation (ZPA). Specific control operations that are not included in the pre-programmed logic routines can be carried out by the user using the ARGEE code-free control logic.«
Select Country
Turck worldwide